Third-party Logistics (3PL) domain expertise

In 1996, Lunatech entered into a partnership with UPS Supply Chain Solutions (UPS-SCS), that led to the development of an innovative supply chain operations household-name global electronics and computer hardware vendors.
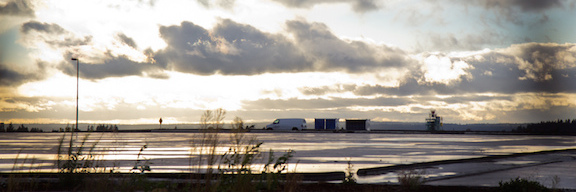
Today, UPS still manages global supply chains electronics products, including warehousing and transport, using a custom IT solution developed by Lunatech that provides end-to-end supply chain visibility. This approach, together with the software that Lunatech developed, enabled UPS to optimise these supply chains and innovate to deliver a unique logistics service.
Lunatech’s specific logistics domain expertise has allowed us to first build a system that supports this supply chain, in the form of a visibility solution. Lunatech further extended this system to support additional business processes, such as automated decision making to select transport companies. For more than ten years, we have continued to collaborate with UPS’ logistics operations staff to further improve the supply chain process, bringing repeated ROI to the business operation.
Third-party logistics (3PL)
To provide some context, consider how a global product distribution supply chain works. This involves various roles for UPS and their customer - the `vendor' who sells electronics or computer hardware.
To work with UPS, Lunatech has to understand how their logistics operation works. As a starting point, consider that the vendor sells electronics, such as communications hardware like network switches, to customers world-wide. One way to think about how this supply chain works is to imagine that the vendor makes the telephones and delivers them to customers. However, in this case the vendor does not own trucks or employ drivers, since shipping is not their core business, so instead they might hire a transport company to deliver the telephones - UPS brown trucks performing deliveries around the world.
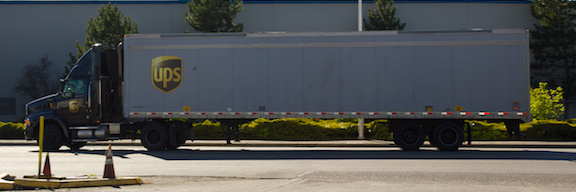
The next step in outsourcing supply chain operations is further outsourcing. Instead of managing their own warehouse, the vendor can outsource the whole logistics operation to UPS, which is called third-party logistics (3PL) because a third-party manages logistics activities, such as transportation, warehousing, inventory management, packaging, and freight forwarding. The usual 3PL set-up would be for the vendor’s stock, e.g. crates of telephones, to be stored in one or more UPS warehouses, and shipped to customers world-wide by UPS.
UPS Supply Chain Solutions (UPS-SCS) is a global third-party logistics (3PL) provider, alongside companies like Companies such as Panalpina, Kuehne + Nagel, DB Schenker, FedEx and DHL Express.
3PL implementations
In 1996, UPS set-up a third-party logistics (3PL) operation for a global communications hardware vendor. This initial implementation involved reporting the delivery status of each shipment to the vendor, to give them visibility of the UPS-managed supply chain. Despite being only the first step in supply chain visibility, this was hard because the warehouse operation did not know when shipments were delivered: they did not have access to information from the transport organisation.
To implement visibility, Lunatech developed a new system that integrated multiple incompatible data sources into a single data model. This enabled the system to generate consolidated delivery status reporting, so that UPS could provide their customer with the delivery information they needed.
In 1997, UPS followed on from the success of the first implementation by providing visibility to another household-name vendor - a global computer hardware vendor. This implementation went further, by integrating information for shipments from multiple warehouses, delivered by multiple carriers (transport companies). This was possible because at this stage, Lunatech understood the supply chain well enough to be able to further develop the visibility platform to handle this additional complexity.
Integrating multiple organisations’ data involves not only data modelling, but integrating incompatible data models in software that translates between them in order to provide a unified view. Outsourcing transport to multiple companies adds significant complexity to the logistics visibility problem, making this a challenging goal. In fact, we can re-state the business goal: to integrate IT for multiple 3PL operations, including both transport and warehouse functions.
Having successfully completed these 3PL implementations, UPS and Lunatech were able to go further by evolving the supply chain business model itself, in a logical extension of the outsourcing behind 3PL.
Fourth-party logistics (4PL)
UPS’s collaboration with Lunatech allowed them to go beyond their 3PL operation: the next step was for the logistics operator itself to outsource logistics services. UPS can use its own transportation to ship world-wide, but in practice it is more cost effective to use different carriers depending on whether you are shipping to a nearby country or halfway around the world. Similarly, depending on the location, there may be alternatives to using a UPS warehouse. When the logistics supplier essentially performs a management function, and uses other suppliers for the various logistics activities, we call this fourth-party logistics (4PL).
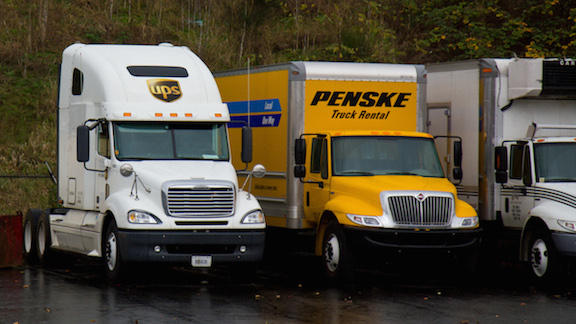
In 2000, UPS introduced fourth-party logistics (4PL) to their customer’s supply chain, managing the complete supply chain from warehouse to transportation and customer-delivery. To achieve this, Lunatech again extended the visibility platform developed for UPS. As well as integrating information from multiple warehouses and carriers, Lunatech integrated with the hardware vendor’s own systems by developing new message-based middleware. At the same time, Lunatech extended the system’s reporting capabilities to generate carrier performance and warehouse activity reports, used for invoicing.
In the 4PL approach, UPS outsources both warehousing and transportation instead of using their own infrastructure, which means that their whole business for their customer - the hardware vendor - is about managing information. 4PL is an information-centric business activity that requires IT systems that capture and directly use a customer-specific domain model, and are integrated with the multiple third-parties whose infrastructure is used.
Lunatech made the 4PL implementation possible by becoming a long-term technical partner and developing significant domain expertise. First, the 4PL required a successful 3PL operation to build on, with the proven IT systems that Lunatech had developed. In addition, UPS could only move to 4PL because they had in Lunatech a technical partner who understood their supply chain domain well enough to collaborate on new models and solutions.
In practice, there are very few 4PL contracts in the supply chain world, due to the difficulty of making it work. Few operations world-wide can deliver on this promise.
Business goals - fourth-party logistics
In 2000, the original business goal of Lunatech’s work for UPS was to implement end-to-end visibility for a 4PL process. This meant developing software to consolidate information about orders and shipments from the many different companies who perform supply chain activities. This kind of visibility is a central challenge in supply chain operations - to systematically gather information companies such as transporters, who may be competing with each other.
Consider a single example: shipment status information. The central information in this visibility system is the status of a given shipment: how far it has progressed through the supply chain, and any problems that have arisen, such as a delay in customs clearance or damage to the shipment. Shipment status updates are a typical area for additional complexity in a 4PL operation, because of differences in the way that different transport companies provide information.
A status update typically includes a shipment reference, a time and location, and a status such as `shipment delayed'. However, not everyone agrees on what a `shipment' is. Consider a delay to a truck containing 200 parcels packed into ten pallets or crates: do you expect one status update, or ten or 200? The answer is that `it depends', which translates to complexity in the IT system that consolidates status updates from multiple transporters into a single view that has a single notion of `shipment' versus `parcel'.
image::vcsplus-shipment-details.png[Supply chain visibility software developed by Lunatech for UPS]
Screen shot: supply chain visibility software developed by Lunatech for UPS.
Results
The result of UPS’ successful collaboration with Lunatech has been to develop IT solutions to unique supply chain problems, which are not handled by standard IT products or even configurable product suites.
The benefit to UPS is clear: this collaboration has enabled fifteen years of multi-million Euro contracts to manage their customers’ supply chains.